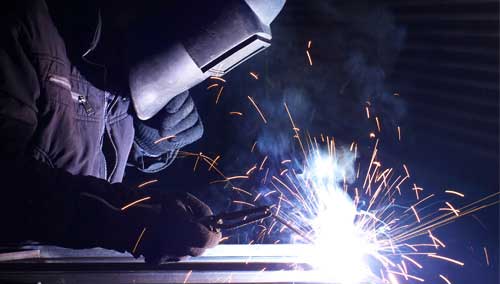
Precision and repeatability define success in metal fabrication. From component design to final assembly, manufacturers across Canada depend on structured workflows to meet tolerance, safety, and application standards. Whether for HVAC housings, appliance panels, or industrial equipment enclosures, precision metal fabrication ensures consistency at scale.
Here are the five core steps fabrication providers follow to deliver reliable and application-ready results.
Step 1: Design and Engineering
The process begins with technical drawings or 3D CAD models that specify product dimensions, tolerances, and structural requirements. Engineering teams assess manufacturability, structural loads, and fitment within broader systems. This phase determines if the part will function properly once fabricated and assembled.
The ability to collaborate during this stage is essential for B2B clients, especially when performance criteria must align with application-specific standards.
Step 2: Material Selection and Preparation
Selecting the right material is critical to long-term performance. Sheet metal thickness, corrosion resistance, weight, and finish all influence functionality. For most applications, mild steel, stainless steel, or aluminum is used based on the environmental conditions or intended use.
Materials are then cleaned, deburred, or levelled to ensure precision during later stages. Fabricators like Weldflow serve clients seeking custom metal fabrication solutions in Toronto and source and process materials according to part-specific specifications.
Step 3: Cutting and Shaping
Once materials are prepared, CNC machines, laser cutters, or punch presses are used to cut, bend, or profile metal sheets. This step translates engineering plans into a physical form with tight dimensional control. The goal is to shape each piece for minimal deviation and maximum repeatability across production batches.
This level of accuracy is what separates qualified sheet metal companies from basic fabrication shops.
Also read: https://www.weldflowmetal.ca/why-use-punching-technology-in-metal-fabrication-processes/
Step 4: Assembly and Welding
After cutting and forming, parts are positioned for fastening, riveting, or welding. In high-volume production, robotic welders may be used to enhance speed and consistency. Welding integrity is especially important in structural or load-bearing assemblies.
Stainless steel and steel assemblies demand different techniques, including MIG, TIG, or spot welding, depending on part complexity and thickness.
Step 5: Finishing and Quality Assurance
The final step involves deburring, powder coating, plating, or painting, depending on the product’s application and client requirements. Every component undergoes inspections for fit, tolerance, and appearance. Functional tests may be conducted for enclosures, panels, or multi-part assemblies.
At this stage, precision metal fabrication delivers on its promise—finished components ready for integration into larger systems or direct use in industrial environments.
The metal fabrication process requires technical planning, material accuracy, and process discipline. Weldflow Metal Products applies this five-step approach to deliver production-ready results for industries across Canada. As one of the trusted providers of custom metal fabrication in Toronto, Weldflow supports every project phase—from design through final delivery—ensuring reliability at every turn. Contact us today to know more.
Also read:
What Are the 3 Main Fabrication Techniques?
Common Obstacles in the Sheet Metal Fabrication Process and How to Overcome Them